October 29, 2018
Good Morning,
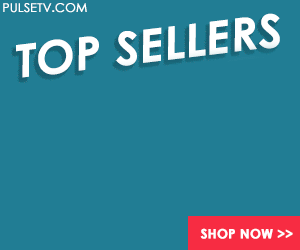
What to be able to manufacture plastic with less cost to the environment? Yes, please!
Learn about this and more interesting stories from the scientific community in today's issue.
Until Next Time,
Erin
P.S. Did you miss an issue? You can read every issue from the Gophercentral library of newsletters on our exhaustive archives page. Thousands of issues, all of your favorite publications in chronological order. You can read AND comment. Just click
GopherArchives
*-- New process could reduce cost of manufacturing plastic --*
Scientists have developed new filtering material that could reduce the environmental cost of manufacturing plastic by separating purified ethylene out of ethane.
By extracting the key ingredient in the most common form of plastic from a mixture of other chemicals, they believe their process consumes far less energy than other methods. The metal-organic framework developed by the National Institute of Standards and Technology was published Friday in the journal Science.
The plastic and petroleum industries manufacture around 170 million tons of ethylene worldwide each year by pulling the material out of a mixture with ethane in the oil refining process.
For years, scientists have been searching for an alternative method to the current high-energy process that cools down the crude to more than 212 degrees below zero Fahrenheit.
Industries would prefer to wring out ethylene, which is the molecule needed to create polyethylene used to make shopping bags and other everyday containers.
"It's very difficult to do," Dr. Wei Zhou, a scientist at the NCNR, said in a press release. "Most MOFs that have been studied grab onto ethylene rather than ethane. A few of them have even demonstrated excellent separation performance, by selectively adsorbing the ethylene."
From an industrial perspective, they would prefer to do the opposite if feasible. "You want to absorb the ethane byproduct and let the ethylene pass through," he said.
Under a microscope, the metal-organic framework looks like a half-built skyscraper of girders and no walls, according to the scientists. The girders surfaces contain certain hydrocarbon molecules that will stick to firmly. A mixture of two hydrocarbons poured through the right MOF can pull one kind of molecule out of the mix and allowing other hydrocarbon to emerge in pure form.
The scientists built their system at the University of Texas at San Antonio and China's Taiyuan University of Technology.
In 2012, other researchers at the NCNR found that a particular framework called MOF-74 separated a variety of hydrocarbons, including ethylene.
"A huge topic in chemistry is finding ways to break the strong bond that forms between carbon and hydrogen," said team leader UTSA professor Banglin Chen. "Doing that allows you to create a lot of valuable new materials. We found previous research that showed that compounds containing iron peroxide could break that bond."
To break the bond in a hydrocarbon molecule, the compound would first have to attract the molecule. By modifying MOF-74's walls to contain a structure similar to the compound, the molecule it attracted from their mixture was ethane.
By using neutron diffraction, they found what part of the MOF's surface attracts ethane.
"Without the fundamental understanding of the mechanism, no one would believe our results," Chen said. "We also think that we can try to add other small groups to the surface, maybe do other things. It's a whole new research direction and we're very excited."
The researchers said they need to further develop the process before it is adapted.
"We proved this route is promising, but we're not claiming our materials perform so well they can't be improved," Zhou said. "Our future goal is to dramatically increase their selectivity. It's worth pursuing further."
*-- Rice scientists say nanotube film could make for better batteries --*
The inclusion of films of carbon nanotubes could be key in building a longer-lasting battery, scientists at Rice University said.
Led by chemist James Tour, the researchers used the nanotube films to come up with a way to halt the growth of dendrites on a battery's unprotected lithium metal anodes, Rice said in a news release Thursday. They published their results this month in the journal Advanced Materials.
The dendrites usually degrade batteries by reaching their cathodes, prompting consumers to avoid lithium batteries in favor of their lithium-ion counterparts because developers can slow dendrite growth in lithium-ion batteries by slowing their charge time, Tour said.
But Tour and his team determined that dendrite growth can be slowed in lithium batteries by using a simple technique that Tour said is highly effective.
"What we've done turns out to be really easy," he said. "You just coat a lithium metal foil with a multi-walled carbon nanotube film. The lithium dopes the nanotube film, which turns from black to red, and the film in turn diffuses the lithium ions."
After 580 charge and discharge cycles with a test battery, the researchers said, full lithium metal cells maintained 99.8 percent of their coulombic efficiency, a phrase used to express the effectiveness at which electrons move in an electrochemical system.
The film was able to maintain a steady level of ions to control dendrite growth by intaking ions from the underlying lithium anode while others were discharged.
"Physical contact with lithium metal reduces the nanotube film, but balances it by adding lithium ions," Rice postdoctoral researcher and paper co-lead author Rodrigo Salvatierra said. "The ions distribute themselves throughout the nanotube film."
Turn Your Backyard into a Tropical Paradise! Get the Solar-Powered Torches Before They're Gone
|
|